INTERSURGICAL CHINA
2020-06-11
-Clear focus on environmental protection, safety, versatility
INTERSURGICAL China is a wholly owned subsidiary of INTERSURGICAL Medical Group, headquartered in the United Kingdom, was established in 1982 and specializes in the manufacture and sale of disposable medical devices and consumables for respiratory anesthesia. Today, the company is a leader in this industry and has numerous offices around the world, including the United States, the United Kingdom, Germany, France, Italy, Spain, the Netherlands, the Czech Republic, Lithuania, Russia, South Africa, Japan and the Philippines. INTERSURGICAL employs more than 3,500 people worldwide and has a turnover of more than 250 million euros.
The high-quality respiratory anesthesia products manufactured by INTERSURGICAL entered the Chinese market in 2008. A direct sales company was established in China in 2010 and a production base was opened in China in 2016 to make the first-class products and services available to more Chinese patients. The factory was expanded at the end of 2019.
The four main product groups are respiratory management, anesthesia, intensive care and oxygen and aerosol therapy.
All of the company’s products have met or exceeded British medical device standards, CE certification of European Union medical devices, US Food and Drug Administration FDA requirements, and have been registered with the Chinese State Food and Drug Administration.
The main product lines – available since the foundation of the company – have been continuously developed until today. In addition, a new airflow generator was developed after the epidemic.
Environmental protection, safety, versatility
While some conventional respirators are PVC, INTERSURGICAL’s products are not made of PVC because it is not environmentally friendly and cannot be broken down. PVC also has a strong inherent odour and contains plasticizers. All INTERSURGICAL product materials are environmentally friendly and safe. Mainly TPE and PP without plasticizers. Only products that use 100% new raw material can guarantee the high product quality.
The masks produced by INTERSURGICAL are suitable for a wide range of people, with ergonomic design and reduced features. The breathing mask has a reinforced ribbed construction and is very light. The product is positioned in the professional, high-quality category. The filter masks can filter up to 99.99% – very effective for corona patients.
Short profile
- Founded in 1982, specialized in products for respiratory anesthesia.
- Four production facilities in Europe, one in China. R&D headquarters in England, assembly plant in Lithuania, Italian clean room production facility.
- The company relies on independence in design, R&D, production and packaging to ensure product quality. Molds are also developed and manufactured internally.
- The product quality is based on the international ISO standards, which are in accordance with EU and national standards.
- Use of PP, TPE and other polymer materials, no plasticizers.
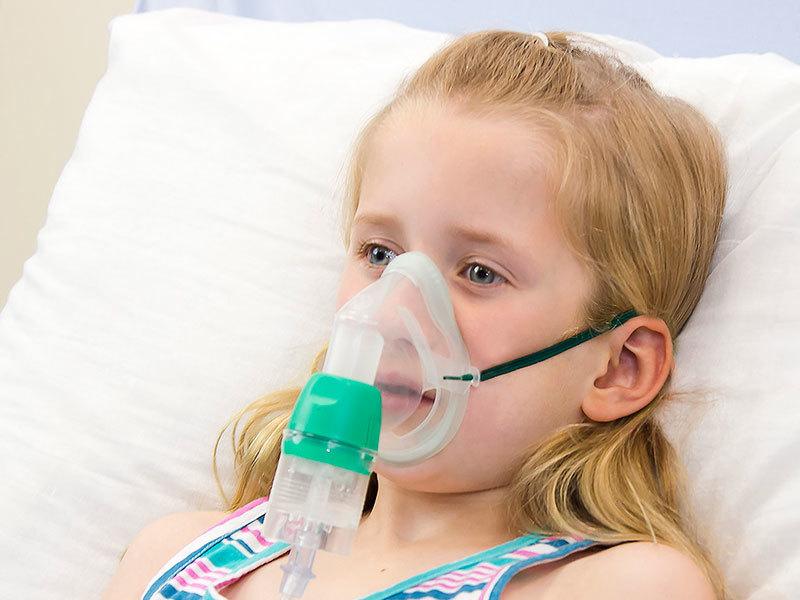
The images of products providing
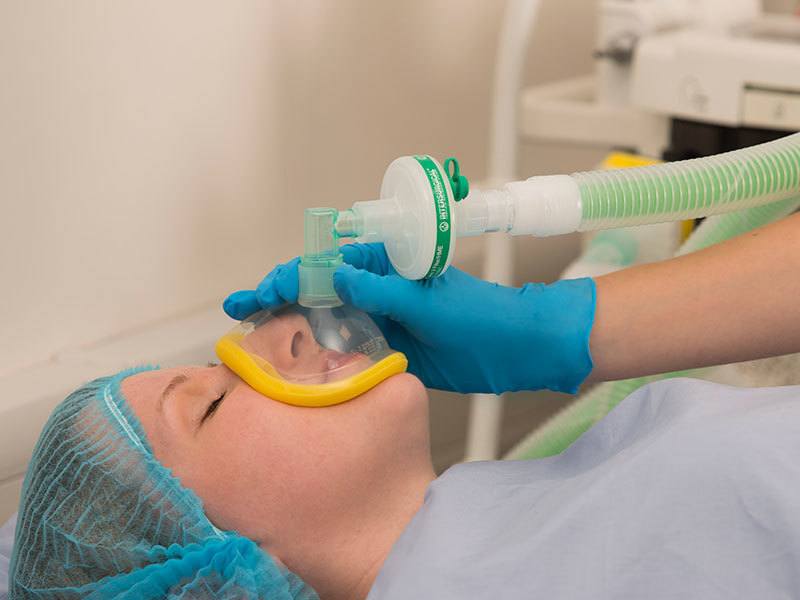
INTERSURGICAL Medical Devices has been dedicated to respiratory anesthesia consumables since its founding in 1982 with manufacturing facilities in the UK, Lithuania, Italy and China. In 2008 INTERSURGICAL entered the Chinese market with its high-quality disposable respiratory anesthesia products and finally established a production base in China in 2016. How did this decision come about?
Li Lingjun, general manager of INTERSURGICAL Changzhou, explains: China has a good investment environment and is the largest market in the world. Investments in China not only cover the Chinese market, but also radiate to the production, storage and logistics centers in the Asia-Pacific region.
In retrospect, the reorganization of factories in China and elsewhere has also proven to be a hedge against the effects of global crisis situations, a hedge against risks in the supply chain.
Is the management system that INTERSURGICAL applies in different factories in the UK, China or Lithuania, Italy, etc. consistent and is a different type of product offered?
Mr. Li: The same management system is used, and the products are classified according to the headquarters‘ plan. Respiratory protection components are mainly manufactured in China. The resulting components are sent to the Lithuanian plant for assembly and from there they are shipped to markets around the world. The Italian plant, which mainly produces STARMED respirators, also played an important role in the outbreak of the new corona virus. Uniform and strict quality management standards are applied worldwide. Lithuania has fully automated warehouses with 50,000 standard pallets, which corresponds to more than 1,000 goods containers that can be delivered to customers in a timely manner. More than 20 million nasal oxygen tubes are produced annually, and each one is tested for blockages and leaks to ensure 100% detection rate of the product. All our products are 100% raw material and are not recycled. This rigor also applies to the selection of our production equipment in terms of respiration. Furthermore, it is very difficult to strictly control the quality of products produced in tens of millions of pieces.
What are the main products that INTERSURGICAL currently offers on the Chinese market and what are the main competitive advantages over other competitors?
Mr. Li: Our main product areas are throat airway management, anesthesia products, critical care products, oxygen nebulization products. We have focused on the supply of respiratory anesthesia machines from the beginning, adhering to integrated management, independent research and development and production. If you follow a strict quality policy and environmental protection, you will always be open to quality innovation and have more choice. INTERSURGICAL focuses primarily on the high quality of its products rather than a price war. All products are 100% tested. Quality always comes first, using 100% raw materials and strictly enforcing quality standards. In China there are more PVC oxygen masks, but we use environmentally friendly PP+TPE material to ensure the high quality of our products. To focus on the brand and the recognition value of the product for the customer.
What are your ideas about the future of the industry?
Mr. Li: With increasing health awareness, more and more people are using nebulization as an alternative to infusion treatment, so the market is looking better and better. It is expected that the market for high-quality respiratory protection consumables will continue to grow. With the epidemic, the biggest challenge lies in the equipment. For the consumer goods industry, the possibility exists that the current category will be able to meet the market demand in the current situation. It’s all about how capacity keeps pace.
How has INTERSURGICAL developed since entering the Chinese market?
Mr. Li: After 40 years of focusing on respiratory products, demand has increased significantly due to the Corona pandemic. INTERSURGICAL’s sales in the Chinese market are growing from year to year at a rate of 30% per year. The Chinese factories are expanding, and additional investments are being made. Sales in the domestic market are almost 100 million per year and the number of employees is over 300. At present, Chinese factories still account for a relatively small proportion of the group’s total production capacity, only 5%, but it is planned to increase this proportion to around 20% in the future.
Has there been any impact on the company’s production and sales since the outbreak of the new corona virus? If so, what are the main aspects?
Mr. Li: The impact of the epidemic on production has been relatively small, and in response to the epidemic, production has concentrated human and material resources on several product categories. Products that were urgently needed to meet the surge in demand. The surge in demand for respiratory products also exerted more pressure on production. INTERSURGICAL is actively working with the government to resume production, recruit new employees and actively meet production requirements. The current capacity of similar nasal oxygen tubes and oxygen therapy products has been doubled.
INTERSURGICAL is one of the first local companies to resume operations. The number of employees has increased by more than 100 and the total number of employees has reached the 300 mark. For example, filters, pulmonary function tests, nasal oxygen tubes, etc., urgent needs and scarce products are being arranged for priority production to help fight the epidemic. INTERSURGICAL’s European plant has not been shut down and has at least doubled its production compared to the past. For some products, capacity has even quintupled. All production sites are being expanded to meet production demand. For example, the Chinese factory, which started with about 200 people, has grown to 300 employees.
As a multinational company, foreign brands may generally be preferred, but INTERSURGICAL began buying electric injection molding machines as early as 2013. The factory in China built with a view to localized production. China is a large manufacturing country and has many equipment manufacturers; consider the advantages of localization.
Why did you choose the Zhafir Venus Series?
Mr. Li: INTERSURGICAL needed a small machine because the process control of the motor is very accurate, and the consistency of the molded products are very satisfying. Then a fully electric machine is clean, energy-saving and environmentally friendly. As a Haitian brand of electric injection molding machines, Zhafir is known for its professional character, which is why we chose it in the first place. The VE 900 kN and VE 1500 kN were bought first.
What is the operating condition of the Venus Series, which has been in operation at INTERSURGICAL for seven years? Has it met your expectations?
Yan Guofeng, manufacturing manager of INTERSURGICAL Changzhou: The Venus Series is currently running stable, without major failures and with relatively few malfunctions. For some minor issues, the appropriate services were available to meet our expected needs. On the whole, we are more satisfied with the accuracy of the equipment, the energy saving effect etc. The quality of the product was good, so we built our own factory and bought additional equipment from CDFA. At present, mainly electrical machines are used for the production of breathing filters and injection molded parts on nasal oxygen tubes, such as small joints etc.
Besides the product itself, technical support is also very important. Can the Zhafir team meet your requirements in this area?
Mr. Yan: So far, I am very satisfied with the service of Zhafir and the technical support is efficient. INTERSURGICAL attaches great importance to regular maintenance of the machines to extend their lifetime.
Are topics like “intelligent manufacturing” or “Industry 4.0” an issue for your company!
Mr. Li: The core of intelligent manufacturing is to realize the computerization and automation of manufacturing companies to achieve the goal of lean, flexible, autonomous, networked and intelligent manufacturing. INTERSURGICAL is also working hard to promote the automation of the assembly process and the digitalization of the production process of components and finally to integrate the whole process.
Does the Corona Pandemic have an impact on product innovation, research and development at INTERSURGICAL?
Mr. Li: It has had an impact as the volumes of some of the Group’s products have increased fivefold. In collaboration with Mercedes and University College London, we have launched 10,000 air generators to provide CPAP for the treatment of Covid-19 patients.
Since the outbreak, what have been the main measures taken by INTERSURGICAL to support the various local actions against the epidemic?
Mr. Li: INTERSURGICAL responded to the call to aggressively resume work, expand recruitment and develop capacity improvement plans within production to meet the surge in demand.
Haitian International is focused on providing „technology to the point“ for its injection molding machine products and solutions, offering customers maximum freedom and flexibility in a time of increasing product innovation and iteration. What are your thoughts on this philosophy?
Mr. Li: The essence of this philosophy is similar to that of lean production, flexible production for the needs of the customer and for mutual benefit. I like it!
Anything else what we can do as your supplier?
Mr. Li: We expect Haitian International to continue to provide quality products and solutions to its customers and achieve a win-win situation. INTERSURGICAL’s products also found immediate application in hospitals in the UK. There is also an active domestic campaign against the disease in the country, with agents donating more than 100,000 protective masks that were shipped from Dubai. Other products support hospitals in several regions. Having strong partners for such business developments is very important to us.