01 Diversified Market & Innovative Drivers
In recent years, the drinkware market has been growing, driven by improvements in living standards, increased consumer health awareness, and product innovation. As seasons change, so does the product line in the drinkware industry. In China, plastic cups dominate the market in spring and summer, while thermal cups are more popular in autumn and winter. The domestic market’s demand is becoming increasingly diversified.
Additionally, innovation and quality improvement have positioned China as a major global producer in the drinkware industry, with rapid growth in both export volumes and overseas demand for various drinkware items.
02 New Demands & New Challenges
With the diversification of market demand, drinkware products have seen innovations in materials, design, and functionality to meet different consumer needs. The injection molding production of drinkware components faces several challenges, requiring higher standards for injection molding technology:
Material Selection: Tritan is currently the preferred material in the drinkware industry due to its safety, odor-lessness, and high transparency. However, Tritan hygroscopic nature imposes strict requirements on the injection molding process.
Its high viscosity necessitates a specially designed screw to ensure optimal material plasticization during the molding process.
Precision Requirements: Thermal cups, which often use a double-layer structure to create a vacuum insulation layer between the inner and outer layers, require precise control of wall thickness during injection molding. This ensures the integrity and uniformity of the vacuum layer and guarantees the perfect fit of seals for optimal insulation.
Precision Injection Molding: High standards for the appearance and details of drinkware necessitate precise control of product dimensions and surface quality during injection molding, avoiding issues like burrs, shrinkage, and deformation.
For lids, surface quality must be flawless, requiring powerful injection and holding pressure capabilities from the injection molding machine.
03 Upgrade: Haitian offers Solutions
In this industry, the injection molding production of drinkware components demands higher standards for processes and equipment. Production efficiency has become a key factor in corporate competitiveness. Haitian MA5 injection molding machines, with their excellent performance and cutting-edge technology, offer specialized solutions for the injection molding of drinkware components, addressing production pain points and injecting new productivity.
Currently, Haitian MA5 drinkware industry application solutions have successfully entered and been applied in the drinkware manufacturing field.
Plastification Component Innovation: Easily Meets New Material Processing Demands
Production managers from leading domestic companies have shared that in response to new trends in material selection, their company decisively chose Haitian MA5 when introducing new equipment. MA5 is equipped with an electric pre-plasticization device and a screw customized for the drinkware industry, breaking material processing limitations, significantly enhancing plastification performance, and easily meeting raw material challenges. This provides strong technical support for the production of drinkware components.
Additionally, the comprehensive upgrade of plastification components has doubled the wear resistance of the equipment, ensuring stability and product quality during long-term high-load production.
HT·XTEND Guarantees Excellent Performance
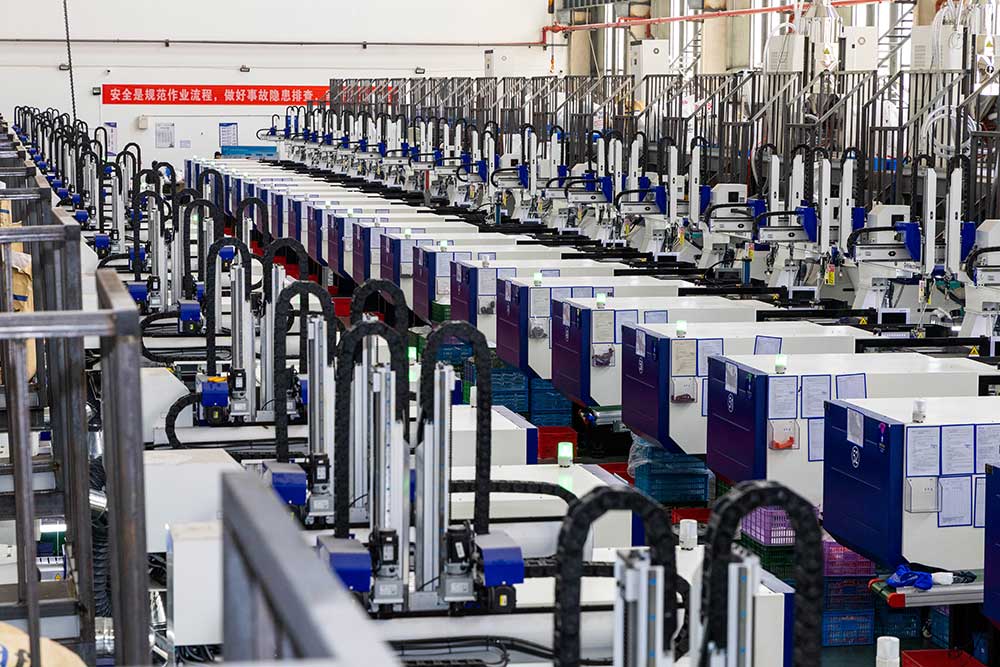
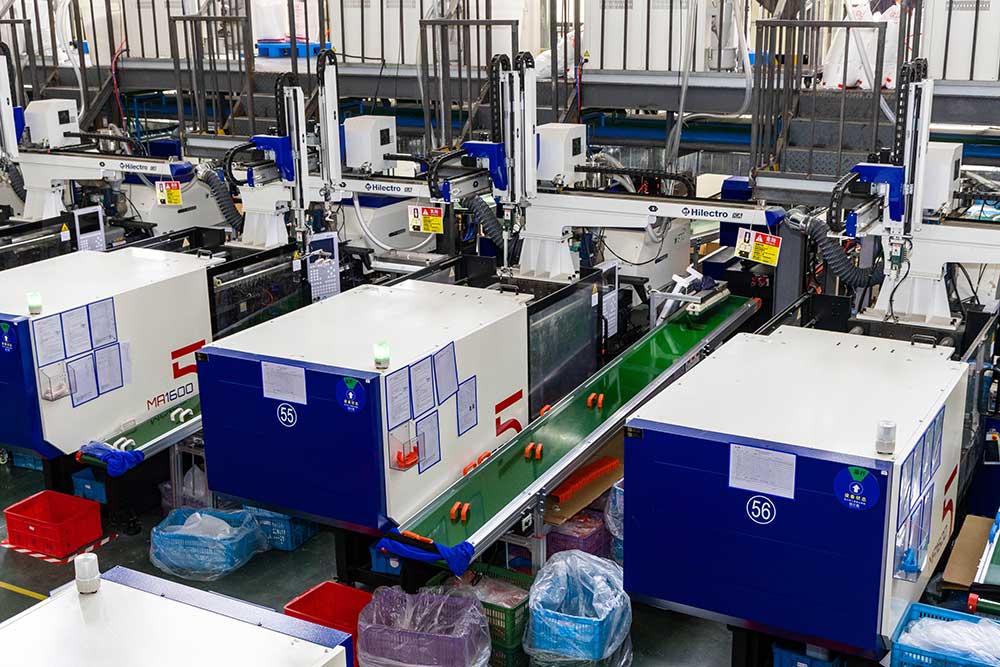
In practice, Haitian’s fifth-generation injection molding machine’s specialized servo power system demonstrates outstanding dynamic response performance and numerous intelligent functions, perfectly meeting the high-speed and high-response demands of drinkware component production. The MA5 also offers stronger clamping force and injection pressure. The clamping unit, using high-rigidity templates and equipped with HT Clamp, ensures precise mold positioning, stable and rapid movements, significantly enhancing production process stability.
Moreover, the comprehensive improvement in injection pressure not only expands the process range to meet production needs but also achieves refined control over injection movement, ensuring product consistency. These comprehensive upgrades enable MA5 to easily meet the high standards for appearance and detail design of drinkware products, precisely controlling product dimensions and surface quality, providing an unprecedented production experience for the drinkware industry.
Intelligent Manufacturing Engine:One-Stop Intelligent Manufacturing Solutions
Drawing on years of experience in the drinkware industry, Haitian International, in collaboration with Haitian Smart Solutions, offers one-stop intelligent manufacturing solutions for industry clients. From plant planning, centralized supply of water, electricity, and raw materials, to deep integration of automation and digital intelligence, it creates a highly efficient, intelligent production environment for clients, fully optimizing the production process, achieving dual improvements in quality and efficiency, and exploring new paths for quality and efficiency enhancement.
Every precise clamping, every accurate injection of MA5, embodies Haitian’s relentless pursuit of excellent craftsmanship and continuous exploration of innovative technology. Haitian’s drinkware industry application solutions aim to make every piece a masterpiece of craftsmanship and design.
In the future, Haitian will continue to focus on technological upgrades and innovation, bringing more high-performance and high-value professional solutions to the drinkware industry. By partnering with clients, we aim to drive the industry’s development hand in hand, bringing more health and warmth to customers’ daily life.