I. Plastic is everywhere in our lives.
While providing great convenience to humanity, it also brings environmental challenges that people have to face. As the concept of environmental protection gradually takes root, how to significantly reduce plastic pollution is imminent. “Circular economy” has handed over a green answer, making all virgin plastics able to be reused. In this case, we can promote more enterprises to use recycled materials as much as possible to reduce waste and thus realize a clean cycle and “new life” of plastic products.
II. The first step in launching the “plastic circular economy” can not be separated from recyclable materials.
ABS is a thermoplastic polymer with high strength, good toughness and easy molding, which is widely used in manufacturing fields such as automobiles, electronic appliances and building materials. In recent years, China’s ABS plastics market demand is huge, and the demand for recyclable materials by enterprises continues to expand, which has driven the technological innovation and development of recycled ABS. However, there are still significant performance differences between regenerated ABS and virgin ABS:
- Preset antioxidants and anti-light aging additives in virgin ABS or modified plastics used in virgin products are consumed during the use or recycling of plastic products.
- The aging and degradation process of plastics may continue to accelerate because after the aging and degradation of polybutadiene, groups such as carbonyl groups and hydroxyl groups will appear, which may further exacerbate aging and affect material properties.
III. Haitian recyclable material solutions
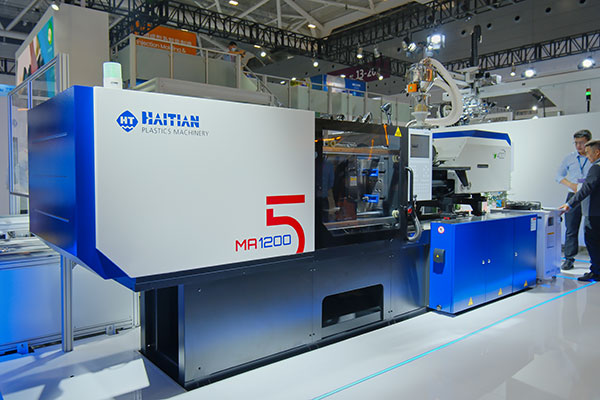
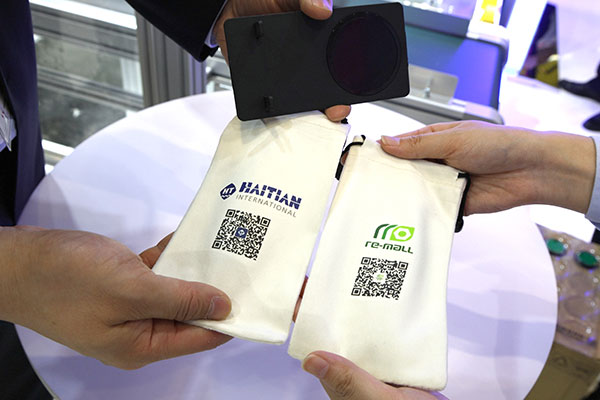
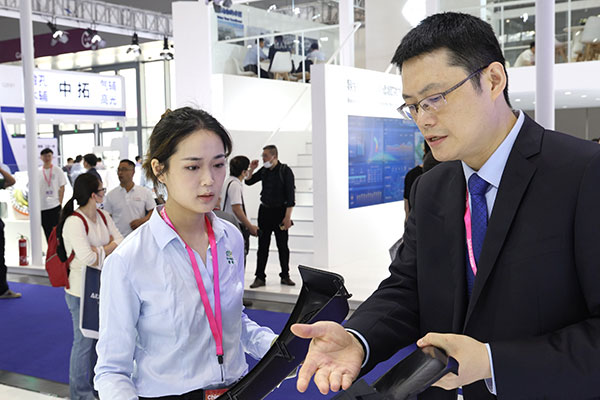
Relying on Haitian’s fifth-generation technology and inheriting the world’s best-selling servo-hydraulic energy-saving injection molding machine, Haitian MA5 solves the production pain points for injection molding of regenerated ABS, and creates a “new life” with excellent performance as the engine.
Product: Wireless Charging Bracket for Cell Phones
In this set of solutions, Haitian MA5 uses 100% regenerated material to make the wireless charging bracket, with the weight of the product of 31g+18g, and the molding cycle of about 42s. The regenerated ABS used in the demo solution is from Shanghai RE-mall, a leading company in the regenerated plastic industry, and both parties are working together to drive the high-quality development of “circular economy”. The specific solution highlights are as follows:
1. Intelligent temperature control to ensure the stability performance of equipment
Pain point: the temperature resistance of regenerated ABS is poor. To ensure the surface gloss and color uniformity of the parts and to avoid defects such as yellowing, the amount of melting plastic should be precisely controlled. At the same time, the residence time of regenerated ABS melt should be as short as possible and the melting speed should not be too fast. Otherwise, the actual material temperature will easily exceed the set value and cause decomposition and color change.
Solution: with a number of innovative technical support and the temperature control system intelligently optimizing the PID control algorithm, MA fifth-generation machine can accurately control the dynamic temperature of each section of the barrel. At the same time, with efficient energy consumption monitoring and analysis, customers can achieve more convenient energy consumption analysis and management, and achieve more ideal energy saving effects.
2. Significantly enhanced plasticizing performance to break the limits of materials
Pain point: There are many sources of regenerated ABS, which can be roughly divided into conventional injection molding, extrusion, heat resistance and flame retardant according to type. The fluidity of extruded materials is lower than that of injection materials. In order to switch the injection virgin ABS of existing molds, the practice of increasing the temperature often has a limited effect on the melting fluidity of regenerated ABS and it cannot solve the problem of lack of injection, but leads to yellowing.
Solution: MA fifth-generation machines bring more powerful performance and smarter control. The whole series is equipped with electric dosing device, the plasticizing performance is increased by more than 20%, the energy consumption is greatly reduced, and the energy saving of the whole machine can reach more than 20%* (depending on the mold condition, the energy-saving effect is slightly different).
3. Increased injection pressure to improve process range and molding capacity
Pain point: High pressure is required for the injection of regenerated ABS. The pressure inside the cavity at the moment of gate often determines the surface quality of the part. If the pressure is too small, the post-shrinkage will be large and the surface shrinkage of the part will be obvious; if the pressure is too large, the surface friction between the part and the cavity will be strong and it will not be easy to release the mold.
Solution: The whole series of MA5 injection pressure is upgraded and the hydraulic system is upgraded to 18.5MPa. The process range meets the production demand of regenerated ABS, making the production of products more relaxed.
IV. The cooperation between Haitian MA5 and regenerated materials comprehensively solves the pain points of recyclable material injection molding, allowing plastics to emit new green power at every moment of “reinterpretation”, opening a new journey for the life cycle of plastic products.
Today, as the green circular economy system is accelerating, the development of economic benefits and recycling technology allows more plastics to be recycled and the production mode of enterprises is reshaped, Haitian will continue to cultivate green production, continue to break through innovation, empower plastic circular economy and pay tribute to the green future.